The Basic Principles Of Alcast Company
Table of ContentsThe 8-Second Trick For Alcast CompanyAlcast Company - The FactsSome Ideas on Alcast Company You Should KnowNot known Facts About Alcast CompanyOur Alcast Company IdeasThe Alcast Company Statements
The subtle difference hinges on the chemical web content. Chemical Comparison of Cast Aluminum Alloys Silicon promotes castability by reducing the alloy's melting temperature and improving fluidness during casting. It plays an essential duty in enabling intricate mold and mildews to be filled up precisely. In addition, silicon contributes to the alloy's stamina and use resistance, making it beneficial in applications where sturdiness is crucial, such as automobile parts and engine parts.It also improves the machinability of the alloy, making it less complicated to refine right into completed items. In this method, iron contributes to the overall workability of aluminum alloys.
Manganese contributes to the toughness of aluminum alloys and improves workability. Magnesium is a light-weight aspect that supplies strength and influence resistance to aluminum alloys.
More About Alcast Company
Zinc boosts the castability of aluminum alloys and helps control the solidification procedure throughout spreading. It boosts the alloy's strength and solidity.
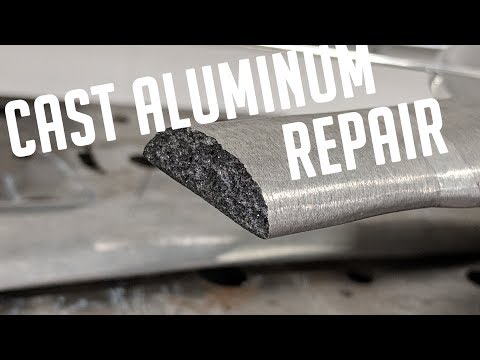
The key thermal conductivity, tensile strength, yield toughness, and elongation vary. Select appropriate resources according to the efficiency of the target item created. Among the above alloys, A356 has the greatest thermal conductivity, and A380 and ADC12 have the most affordable. The tensile limit is the contrary. A360 has the very best yield strength and the greatest elongation rate.
Not known Details About Alcast Company

In accuracy casting, 6063 is appropriate for applications where detailed geometries and high-quality surface area coatings are critical. Examples consist of telecommunication enclosures, where the alloy's premium formability enables for sleek and cosmetically pleasing layouts while maintaining structural honesty. In the Illumination Solutions industry, precision-cast 6063 components produce sophisticated and efficient lighting fixtures that need complex forms and excellent thermal performance.
It causes a better surface area finish and much better deterioration resistance in A360. Moreover, the A360 exhibits exceptional elongation, making it optimal for facility and thin-walled components. In accuracy casting applications, A360 is appropriate for sectors such as Consumer Electronic Devices, Telecommunication, and you can check here Power Tools. Its boosted fluidness permits elaborate, high-precision components like smart device housings and communication device real estates.
Getting The Alcast Company To Work
Its unique properties make A360 a valuable selection for accuracy spreading in these sectors, boosting item resilience and high quality. aluminum foundry. Light weight aluminum alloy 380, or A380, is a widely used casting alloy with several distinct characteristics.
In precision spreading, aluminum 413 shines in the Customer Electronics and Power Tools sectors. This alloy's exceptional corrosion resistance makes it an exceptional selection for exterior applications, guaranteeing resilient, durable items in the mentioned sectors.
Facts About Alcast Company Revealed
When you have actually chosen that the aluminum pass away casting process is appropriate for your job, an essential following step is choosing one of the most suitable alloy. The light weight aluminum alloy you choose will significantly influence both the spreading process and the homes of the last product. Due to this, you need to make your choice thoroughly and take an enlightened technique.
Determining the most ideal aluminum alloy for your application will certainly imply weighing a large array of features. These relative alloy characteristics adhere to the North American Die Spreading Association's guidelines, and we have actually split them into two categories. The initial category addresses alloy characteristics that influence the production procedure. The second covers features affecting the buildings of the end product.
Alcast Company - Questions
The alloy you select for die casting straight affects several facets of the casting process, like how easy the alloy is to deal with and if it is vulnerable to casting issues. Warm fracturing, also known as solidification splitting, is a typical die casting problem for aluminum alloys that can lead to inner or surface-level splits or cracks.
Certain light weight aluminum alloys are much more at risk to warm cracking than others, and your selection needs to consider this. One more typical problem located in the die casting of light weight aluminum is die soldering, which is when the actors sticks to the die wall surfaces and makes ejection challenging. It can damage both the cast and the die, so you should look for alloys with high anti-soldering residential or commercial properties.
Deterioration resistance, which is already a significant quality of light weight aluminum, can differ considerably from alloy to alloy and is a vital characteristic to think about depending upon the ecological problems your item will certainly be exposed to (Foundry). Use resistance is one more home typically looked for in light weight aluminum products and can differentiate some alloys